How Digital Twinning is Changing the Industry 4.0 Landscape
Tech Innovation
May 2019
As manufacturing plants are moving towards smart automation, digital twinning is becoming more widely discussed and implemented. Digital twins are important for investigating and training processes and parts of industrial plants, and to understand movement throughout the supply chain – in addition to monitoring and predicting performance in real-time and allowing for “what-if” scenarios. By accurately visualizing processes and how they work, users have a better approach with regards to the production process, streamlining and automating where prior to the advent of AI and ML had not been possible.
A leader in digital twinning and production optimization is Seebo, who works across the globe with industrial clients to optimize quality and predict and prevent manufacturing disruptions. Start-Up Nation Central had the pleasure of sitting down with Lior Akavia, CEO, and Oren Ezra, CMO, to discuss their marketing strategy, why they decided to pivot into the Industry 4.0 sector, and the challenges they faced as a result of this.
What is the origin of Seebo – how did it all start?
“Prior to founding Seebo, we founded (and later sold) a company that manufactured physical video game accessories, in China. We noticed that both physical and digital interactions were integral to gaming accessories (for example, Wii), yet there were no tools that could help us understand the complex integration between the two. It seemed clear that there was a market for manufacturers who were interested in implementing IoT in their consumer products, and required such tools – and this was how Seebo came about.”
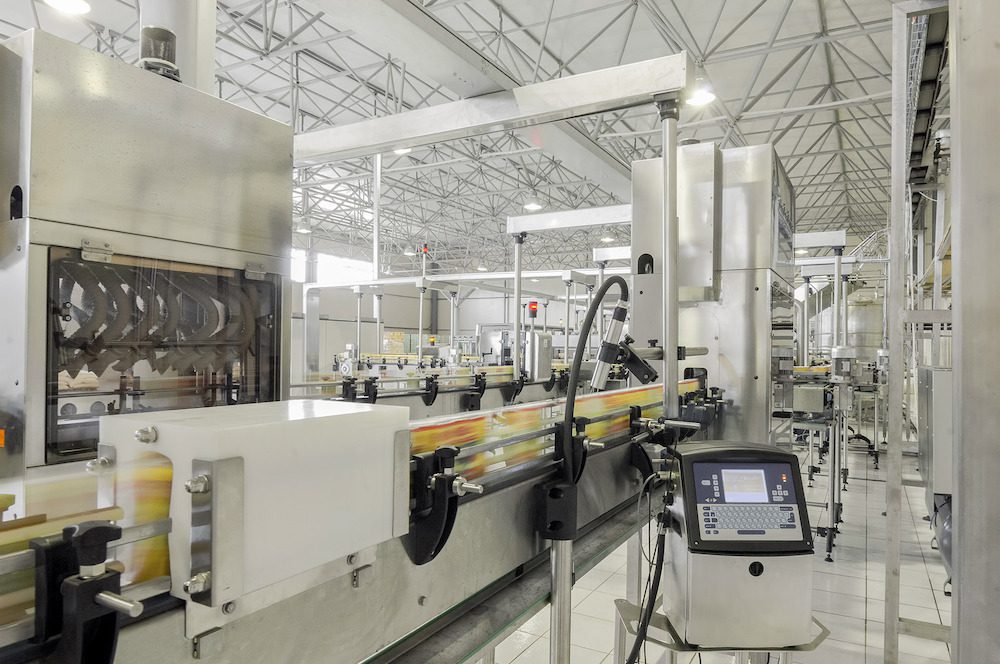
Why the pivot from Consumer IoT to Industrial IoT?
Many industrial manufacturers face challenges related to the quality of the product, wasted resources, downtime, limited throughput, and more.
IoT is transforming the industry and has resulted in the significant growth of IIoT. One of the reasons why the adoption of IoT is higher in the industrial sector, is that largely speaking, industrial plants are already automated. “This enabled a relatively easy connection of our solution to a network which already has sensors in place, and to which we can apply advanced analytics.”
“Our solution was built to support very complex IoT systems, which are capital-intensive, and we saw the opportunity to pivot into industrial IoT where we could generate even greater value for our clients. By applying our technology to the production floor of large manufacturing facilities, we seized the opportunity to provide production teams with real-time visibility into their production lines, and actionable insights to help solve all kinds of manufacturing-related challenges.”
Seebo’s IIoT solutions offers production teams a production-line digital twin with automated root cause analysis and predictive alerts that drive users to action, helping achieve continuous improvement in throughput and quality.
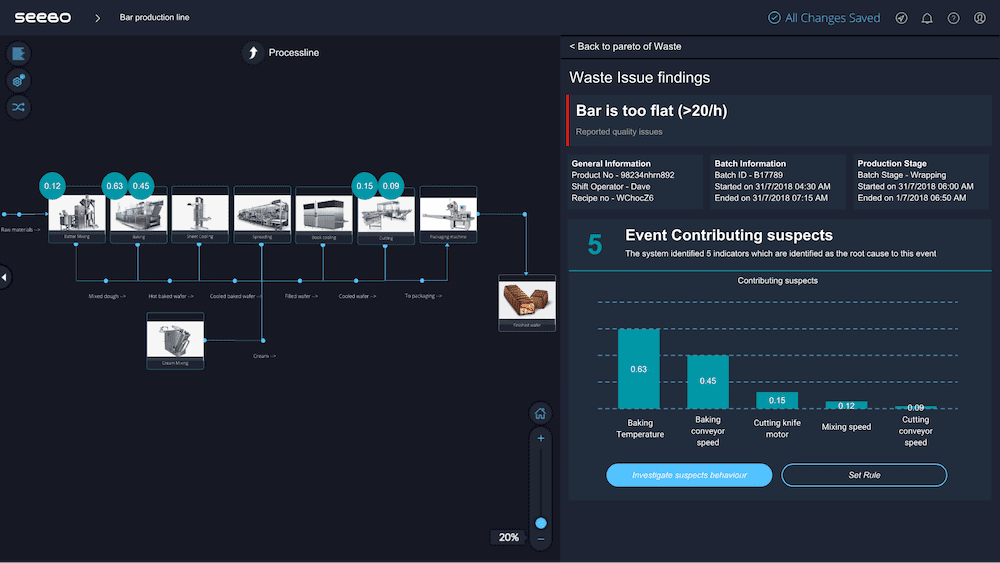
What makes your technology unique?
“When a new industrial manufacturing client starts to work with us, we use our twin modelling tool to capture the way the production process works, which is done very quickly, in only a matter of hours. Once the production data is captured, we bring the sensor data into the context of the process, which allows us to run machine learning algorithms in a context-reliant manner, which generates more accurate results. We then visualize the results of our analytics within a graphical, interactive digital twin of the production process, enabling us to deliver the results in a very intuitive and actionable way to the users in the factory. When it comes to process manufacturing, Seebo is accurate, actionable and easy to use.
Imagine a virtual model of the production line on one side, with the insights on the other, and when you click one of the machines in the line to analyze its performance, the insights change accordingly. The Seebo platform works on a what-when-how basis: providing predictive alerts, automated root cause analysis, and a simulation of how to handle the issue. This is a process far broader than predictive analysis, as the technology is able to predict losses in production yield and quality way ahead of any resulting fail effect.
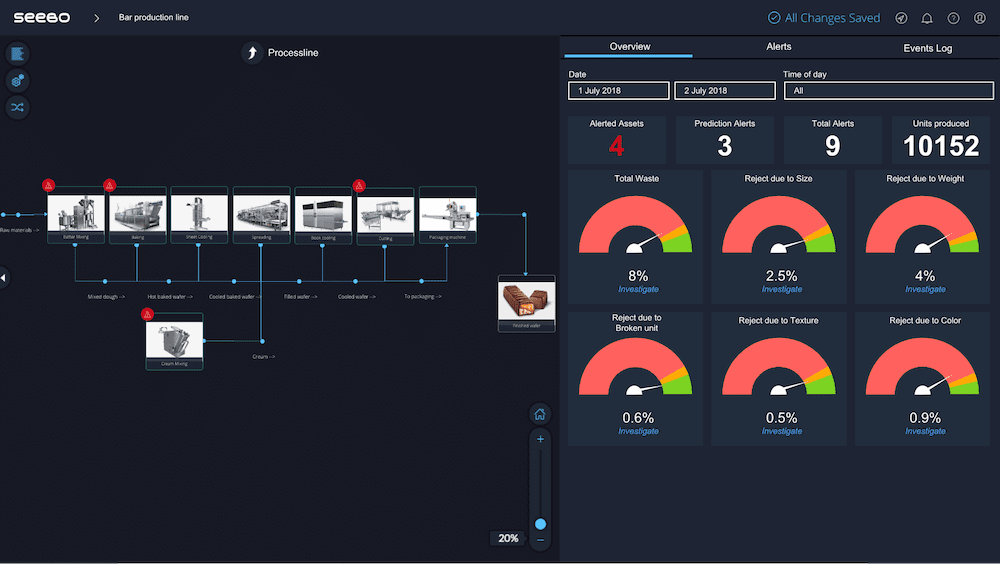
What lies ahead for Seebo?
“We actually feel quite privileged in that we are contributing to a greater mission – that of enabling manufacturers worldwide to support the world’s growing demands in the right way.”
Over the next 30 years, the world population is set to grow by 3 billion. On top of this, third world country consumption is beginning to more resemble that of first world countries, so manufacturers will need to produce at a dramatically increased rate.
“Such an increase means increased risk, by which we mean that if we do it properly, we can live in a world which is green, cost of living affordable contained and sustainable, healthy – but if we don’t, we can expect a world that is polluted, expensive, unhealthy and unsustainable, which is a big responsibility.
The good news is that tech is on our side. Hyper trends such as Big Data, IoT, and AI are setting the stage for effective manufacturing. AI will also empower production experts in a way which will be able to help save billions of dollars a year. Together with other companies in the market, we are part of a bigger picture to affect and improve the quality of life for our children and grandchildren.”
To download the latest map and get more insights on the Industry 4.0 ecosystem, click here